To chat to Paul Sohi is to geek out over all things 3D printed. He takes me on a journey from 3D printed mannequins (the subject of his PhD) to a new polycarbonate composite prosthetic leg he is developing with a team spanning half a dozen countries but centred at Autodesk in San Francisco, for an Olympic cyclist bound for Rio later this year. It's a helluva ride, so buckle up!
What initially prompted me to get in contact with Paul was a question I've been pondering whilst working at the fringe of fashion and technology for some time. Why aren't there robot models? And why don't I create the first robot modelling agency? It makes sense for so many reasons, but more on that in a later post.
Paul's research and development at the Royal College of Art in conjunction with the Makerversity at Somerset House centres on solving an immense problem in mannequin manufacturing. Mannequins are currently sculpted by hand before being moulded and cast - a time consuming process which imposes mass standardisation. As someone who has hired mannequins for London fashion week I can attest to the limited offer currently on the market.
Consider a museum requiring a custom-sized mannequin to display historic clothing, and then consider a new technology allowing such a mannequin to be 3D printed in days rather than laboriously hand made in months. Then consider that currently, the best way of creating mannequins to display such costumes is to 3D scan the clothing to determine the volume inside of them when worn on which to then base a mannequin shape - requiring reverse-engineering of the mannequin to mimic someone that did actually live and wear those clothes at a point in historical time.
It's on consideration of these weird truths it's possible to begin seeing the benefit of Paul's creation of an algorithm designed to transform actual body (or garment) measurements into 3D printed mannequins, rather than relying on artistic creations inspired by - but anatomically untrue to - the human body. The key here is that measurements entered into Paul's program are manipulated and represented visually in line with actual metamorphic landmarks. For example, height has an impact on body proportions.
It is incorrect to simply scale a mannequin up or down directly proportionately - there are intricacies in height ratios that Paul's rigorous algorithm takes into account so that the mannequins he 3D prints are true to the human form, rather than a sculpted representation of an imagined ideal. Shorter people's legs are proportionately longer than their torso compared to taller people, for example, but you would not detect this by looking at them - both body proportions simply look 'right'. Herein lies the difficulty in artistically interpreting the human form where size and fit are concerned.
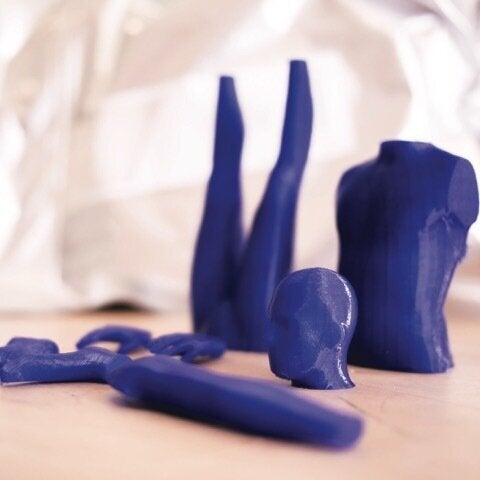
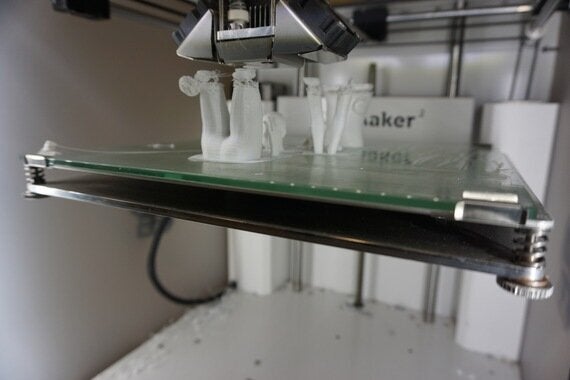
Paul's 3D printed scale mannequins being printed in parts for later assembly
The motivation behind Paul's PhD was to find out if he could create a 3D printed mannequin using mass customisation algorithms built upon an immense amount of research underpinned by the International Standards. These standards provided all the necessary body measurements to create a digital mannequin which can then be 3D printed.
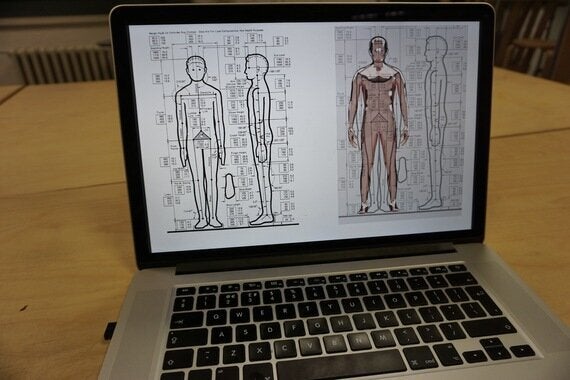
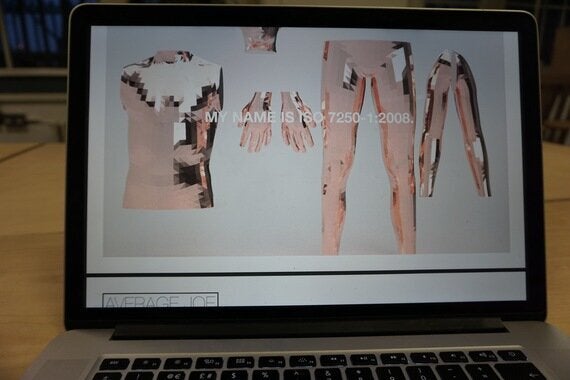
International Standards
An important point made by Paul during our conversation is that mass customisation via 3D printing is now possible on a production scale - it has evolved beyond prototyping. This means that standardisation of mannequins is no longer necessary and the skilled work required for each fashion retail market does not have to be localised. Since a 'standard' size small in Asia is nothing like a 'standard' size small in Europe, mass customisation shatters geographical boundaries and means standardisation - at best badly sized and limited in terms of body shape and at worst pushing damagingly unrealistic body ideals - is no longer necessary.
The mannequins Paul is developing can be tailored according to cultural specificity. Regional cuisine radically effects body shape, size and proportion and genetics also has a considerable impact. These factors can be taken into account in Paul's algorithm.
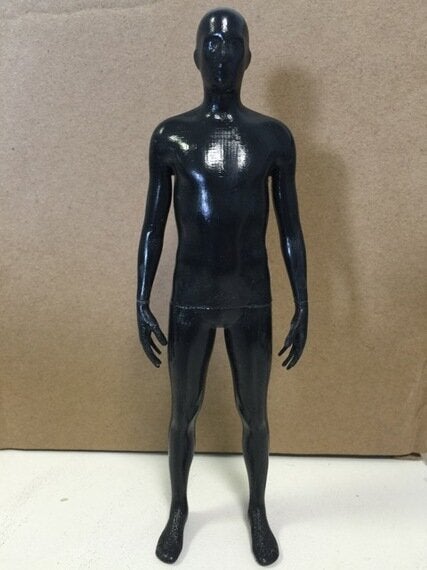
A complete 3D printed scale mannequin
From an aesthetic point of view, every fashion brand has its own ideal mannequin which in some cases may be seasonal. These are made from master moulds and if done by hand using current methods, take months. 3D printing takes a fraction of the time, allowing greater flexibility and mannequin diversity.
Paul describes his work as creating avatars and body forms. He is currently working with the Victoria & Albert Museum, London to find rapid solutions for mannequin making for display of historic costumes. As an extension of this revolutionary development for display mannequins, Paul is looking at how the current mass standardisation of garment making mannequins relates to sizing within the fashion industry.
There is no datum on mannequins - no system for sizing and no standard approach to it across the industry. When creating clothing, we have anatomical landmarks (nape to waist, for example) but the way this is measured is still variable. Paul is determined to standardise measurement taking and sizing to put an end to what is a slow, laborious and repetitive process. He makes the point that, for example, three people in the fashion industry will measure the same dress and get three completely different sets of measurements . Compare that to Architecture - or any other creative industry - and you would be laughed at for not having and applying a set of standards. He makes a strong point and I have personally dealt with this often painful aspect of sampling and production in the fashion industry. Paul is confident that a set of standards can be extrapolated from the points mapped in his algorithm.
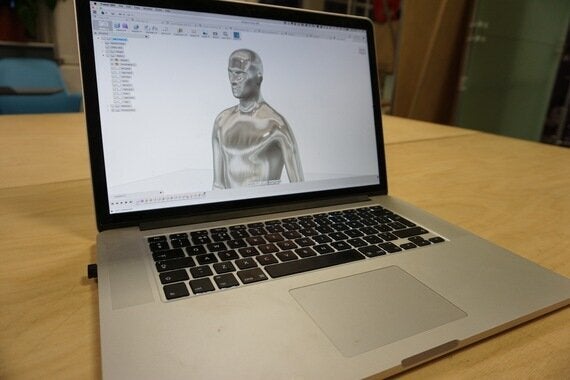
Interestingly, Paul tells me that the standard nape to waist measurement of garment making blocks used routinely in the fashion industry came from 1920's military uniforms. Today's approach to garment sizing and pattern proportions has only marginally evolved since then. 'Standard sizes' are in truth specific to each individual fashion house and are not related to any actual standard, which to me makes sense because each fashion house/brand has it's own silhouettes and 'fit' which are part of its aesthetic, but I can see how this isn't customer friendly and how in an increasingly e-commerce driven industry sizing standardisation would reduce returns and help consumers make better style choices.
Returning to museum mannequins, the Alexander McQueen exhibition Savage Beauty at the Metropolitan Museum of Art in New York was one of the most successful exhibitions of all time, but despite this, when it ended it was not picked up immediately by another institution. The hand-sculpted mannequins, made specifically for the garments they displayed were destroyed. Shortly after, the V&A took on the exhibition, and set about hand-making the mannequins all over again. Almost a year later they were complete. If these had been created using Paul's 3D printing method this would have been simpler, quicker and less expensive.
The exception within the Savage Beauty exhibition was the Plato's Atlantis 3D printed mannequins which closed the exhibition. See the 3D rendering by Asylums FX and a photo I took at the exhibition below:
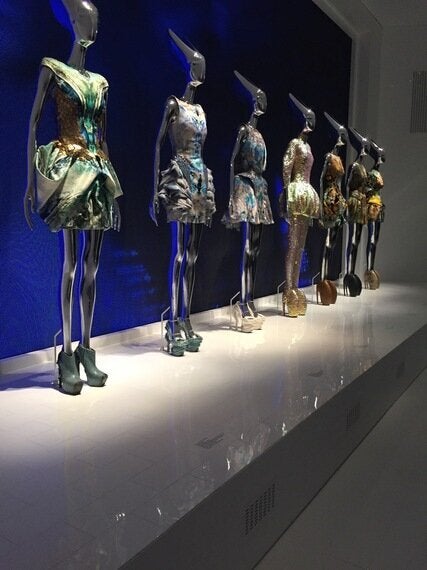
Plato's Atlantis, Savage Beauty, Victoria and Albert Museum, London
When I ask Paul about the response so far to his work he says it has been met with distrust and caution from a number of museum curators and fashion designers who feel things are working just fine as they. The fashion industry is famously and paradoxically resistant to change (the out-of-synch seasonal cycles and some luxury brands still refusing to sell online are just two examples) but why isn't the way things are done being challenged? Why can't we do things better? Why can't we explore technology to do things in a better way? As long as we pose the questions, it appears technology will provide the answers.
Paul and I leave the Makerversity disagreeing over the recent Batman V's Superman film (he's a fan, I'm not) and agreeing on the amazingness of The Hulk. I wish him well on his bumpy but worthwhile journey to fashion mannequin disruption.
Follow me on Instagram: @techstyler