While cities and businesses across the country move to cut down on ocean pollution by banning plastic straws, there’s an even bigger plastic crisis devastating marine ecosystems ― and most of us aren’t aware of it.
Each year, millions of tons of plastics end up in the oceans. Drinking straws are thought to make up less than 1 percent of that debris. By comparison, commercial fishing fleets lose or abandon more than 700,000 tons of plastic nets, lines and traps ― an estimated 10 percent of the plastic waste in the oceans and seas.
Known as “ghost gear,” abandoned fishing items can be practically invisible in dim, underwater light, and each year they entangle and kill millions of marine animals, including sharks, dolphins, seals and turtles. The plastic these nets are made of will linger below the surface for hundreds of years, slowly degrading into small fragments and becoming part of the food chain. What’s more, there is no registry for fishing gear like nets, so ghost items can’t be traced back to the owner, allowing commercial fishers to escape accountability.
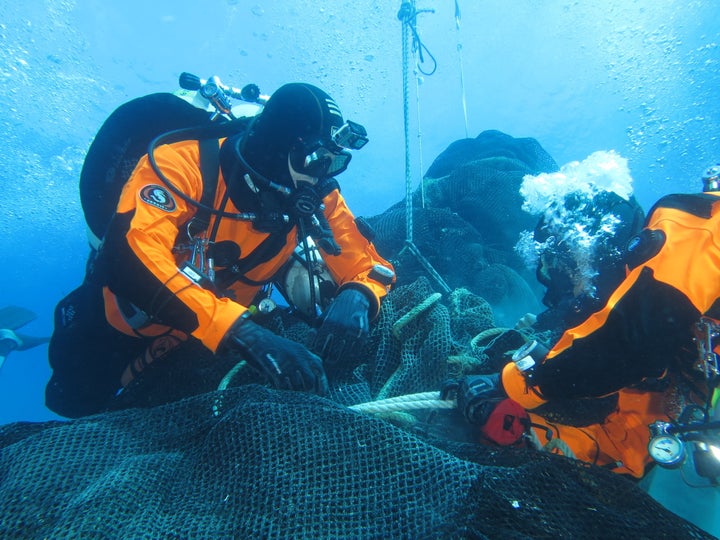
Cleaning up ghost gear is difficult and costly. When nets are recovered, they are often sent to landfills or incinerated, which represents a missed opportunity to recover the plastic. But cleanup efforts sometimes pull tons of netting out of the ocean that can be repurposed into textiles and other consumer goods.
On Oct. 8, that’s exactly what happened when a team of volunteers recovered a gigantic ghost net off the coast of the Aeolian Islands, near Sicily.
The mass of twisted nylon weighed nearly 3 tons and measured 650 feet long. It once made up part of an aqua-culture fish farm project that was destroyed in a storm over a decade ago. Weighed down by sand, the abandoned net sat more than 100 feet below the surface.
Marine animals have learned to avoid the area around the net, and frustrated local fishermen have repeatedly tried to remove it, to no avail. It was simply too great a task to cut it into pieces and haul it to shore.
Healthy Seas, a global initiative that removes plastic waste from the oceans and recycles it into textile products, thrives on this type of challenge. The organization launched three boats ― containing six divers from the Netherlands, two Italian divers and three local fishermen ― from a harbor on the island of Lipari. They had spent the previous two days recovering about 2,000 pounds of plastic fishing waste from the crystal blue waters, including scores of nylon fishing lines that were coiled like plates of spaghetti on the harbor seabed.
When the team reached the ghost net, the divers cut it free, bundled it together with rope and attached a series of lift balloons. The years of debris caught in the net made it too heavy for the boat winch to take the strain, and the three fishermen leaped into action, grabbing and hauling it into a boat. It was painstaking work, and sometimes the net looked in danger of sliding back into the water.
“The net’s not out until it’s out,” Veronika Mikos, the project coordinator, repeated as she watched them work.
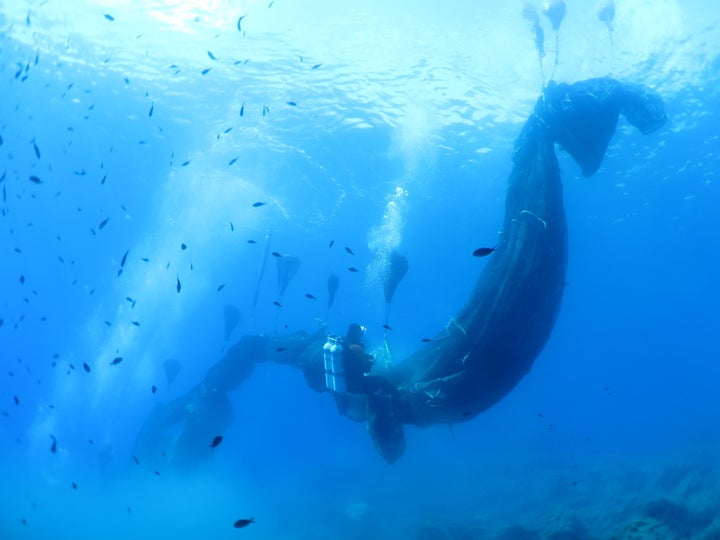
After nearly an hour of grabbing and heaving, the last fold of nylon was in the boat. Divers and fishermen high-fived. The monster net, the biggest continuous net Healthy Seas has brought to the surface to date, was out of the ocean.
But the saga wasn’t over. The next phase of the plan was to clean and ship the net to a factory in Slovenia, where it will be turned into clothing. Aquafil, an Italian company, funded Healthy Seas’ expedition and plans to turn the netting into Econyl, a regenerated nylon fiber made from recycled plastic polymers.
Worldwide, there are a number of initiatives similarly removing and recycling ghost gear and other marine debris. Aquafil CEO Giulio Bonazzi said his company’s methods are different from most.
Usually, recycling plastic requires a mechanical process: chopping the plastic into small flakes and turning it into pellets that can be used to make low-grade plastic products, including flowerpots and trays for food packaging.
But Aquafil uses a chemical form of purification that takes the fishing net back to its original form: oil. According to Aquafil, this uses 80 percent less energy than making nylon from virgin oil. And it makes high-quality, high-performance yarn that clothing brands have used in complex products like bikinis, athleisure apparel and sundresses.
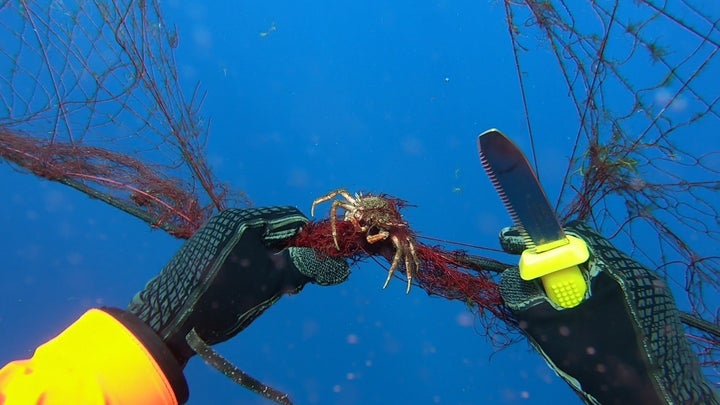
Huge fishing nets can yield enough yarn to make thousands of garments.
But recovery efforts like the one Healthy Seas pulled off last week aren’t always feasible. Demand is high for fishing gear made from cheap, mixed-plastic polymers, which are difficult to recycle.
“There are two things that need to change,” Bonazzi said.
First, he said, “nets must only be made from plastic polymers that we know we can recycle into something useful and desirable. We must keep it simple.”
And, second, nets should not become ocean waste to begin with.
“There needs to be a global registry of fishing gear. When the fishing communities buy their nets, it is logged and registered, and at the end of the useful life of the gear, they are responsible for returning it for recycling,” he said.
“There is no reason for ghost nets,” he added. “We should be able to recycle 100 percent of nets. We have the capacity; we have the technology.”
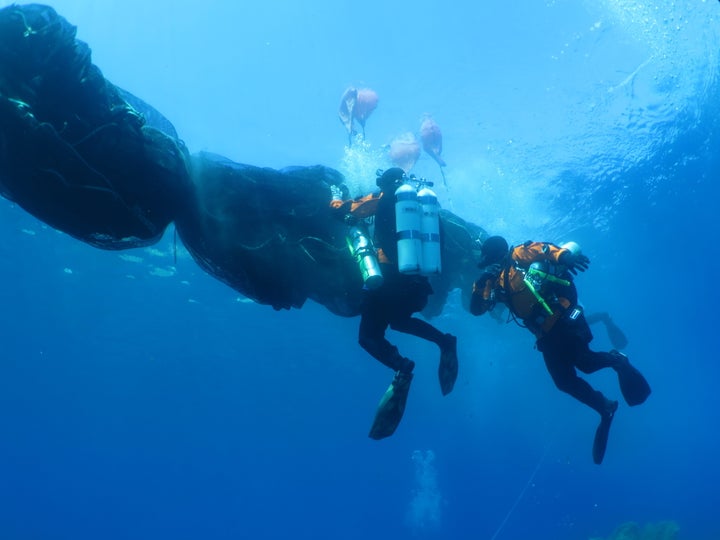
This story is part of a series on plastic waste, funded by SC Johnson. All content is editorially independent, with no influence or input from the company.