Solar panels are becoming cheaper, there’s no doubt about that.
However, even at their cheapest they’re seen as being hard to justify for many.
Well now professor Paul Dastoor and his team at the University of Newcastle, Australia believe they have the answer: A printed solar panel.
Unlike conventional glass panels, professor Dastoor’s are printed using a special electronic ink onto the same material that’s used to make cola bottles.
That makes them flexible, light, quick to produce and more importantly, cheap.
“No other renewable energy solution can be manufactured as quickly. On our lab-scale printer we can easily produce hundreds of metres of material per day,” explains professor Dastoor.
“If you had just ten of these printers operating around the clock we could print enough material to deliver power to 1000 homes per day,”
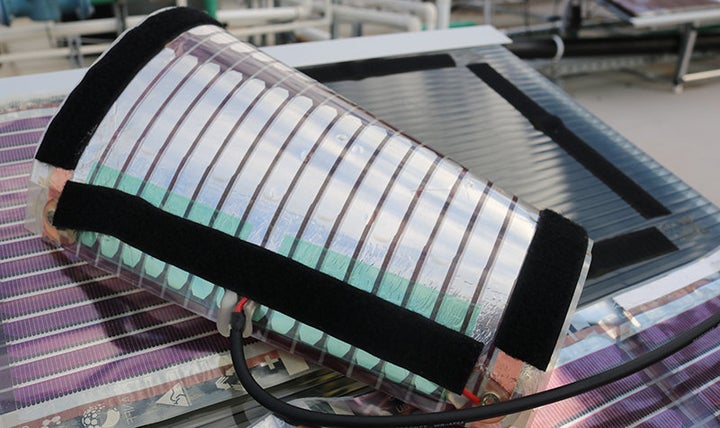
It’s a bold claim, and one that comes with a caveat. Unlike Tesla’s Solar Roof, professor Dastoor don’t know how durable their panels are.
That testing begins now, with a huge 100 square meter array that will help determine the lifespan of the panels and also their efficiency over long periods of time.
Dastoor isn’t primarily looking to compete with Tesla’s bespoke service, instead he sees these panels as being mass produced options for small deeply rural communities that have never had access to electricity before. Then there’s his home country of Australia.
“The low-cost and speed at which this technology can be deployed is exciting, particularly in the current Australian energy context where we need to find solutions, and quickly, to reduce demand on base-load power.” explains Dastoor.
To help accomplish this the panels are incredibly cheap at just £7.60 per square meter.
Making the panels is a remarkably simple process. The panels are made by printing an advanced electronic ink directly onto clear laminated sheets.
There’s no special printer involved either, the sheets are created using a conventional printing process.
Since 2013 the university has been perfecting the creation of the materials needed and it’s now able to produce them at scale.
The next step for the team is of course testing. This will allow them to properly gauge the performance of the panels.